Robotics
Researchers Training Plastic to Walk Under Light
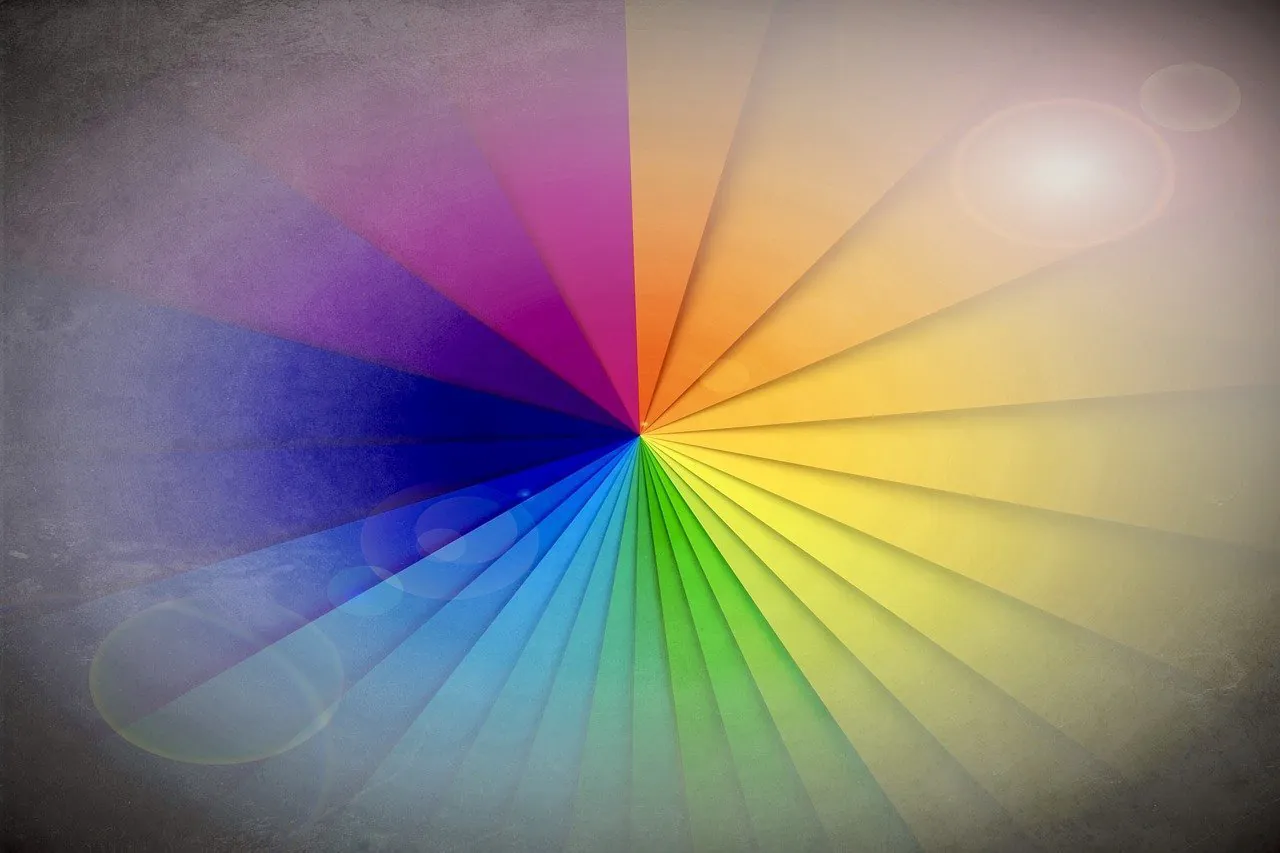
Researchers in Finland are currently working on developing and âtrainingâ pieces of plastic to be commanded by light. This is the first time that a synthetic actuator, in this case thermoplastic, is able to âlearnâ how to do a new action, in this case walking, based on its past experiences and not computer programming.
The plastics in this project are made from thermo-responsive liquid crystal polymer network and a coat of dye. They are soft actuators that are able to convert energy into mechanical motion. The actuator was at first only able to respond to heat, but that is changing since light can be associated with heat. Because of this, the plastic is able to respond to light. The actuator is somewhat flexible and bends itself in a similar way that a human bends its index finger. When the actuator has light projected onto it and therefore becomes heated, it âwalksâ similarly to an inchworm, and it moves at a speed of 1 mm/s, or the same pace as a snail.Â
Arri PriimÀgi is a senior author of Tampere University.
“Our research is essentially asking the question if an inanimate material can somehow learn in a very simplistic sense,” he says. “My colleague, Professor Olli Ikkala from Aalto University, posed the question: Can materials learn, and what does it mean if materials would learn? We then joined forces in this research to make robots that would somehow learn new tricks.”Â
Other members of the research team include postdoctoral researchers Hao Zeng, Tampere University, and Hang Zhang, Aalto University.Â
There is also a conditioning process that associates light with heat, and it involves allowing the dye on the surface to diffuse throughout the actuator, which turns it blue. The overall light absorption is increased, and the photothermal effect is increased as well. The actuatorâs temperature also raises, and it then bends upon irradiation.Â
According to PriimĂ€gi, the team was inspired by another well-known experiment.Â
“This study that we did was inspired by Pavlov's dog experiment,” says PriimĂ€gi.
In that famous experiment, a dog salivated in response to seeing food, and Pavlov then rang the bell before giving the dog food. This was repeated a few times, and the dog eventually associated food with the bell and started salivating once he heard the bell.Â
âIf you think about our system, heat corresponds to the food, and the light would correspond to the bell in Pavlovâs experiment.â
“Many will say that we are pushing this analogy too far,” says PriimĂ€gi. “In some sense, those people are right because compared to biological systems, the material we studied is very simple and limited. But under the right circumstances, the analogy holds.”
The team will now increase the complexability and controllability of the systems, and this will help find certain limits of the analogies that can be drawn to biological systems.Â
“We aim at asking questions which maybe allow us to look at inanimate materials from a new light.”
The systems can do more than just walk. They are able to ârecognizeâ and respond to different wavelengths of light that correspond to the coating of its dye. Because of this, the material becomes a tunable soft micro-robot that is capable of being remotely controlled, which is extremely useful for biomedical applications.Â
“I think there's a lot of cool aspects there. These remotely controlled liquid crystal networks behave like small artificial muscles,” says PriimĂ€gi. “I hope and believe there are many ways that they can benefit the biomedical field, among other fields such as photonics, in the future.”