Robotics
Researchers Develop Tiny “Spinobots” with Rat Muscle and Spinal Cord Tissue
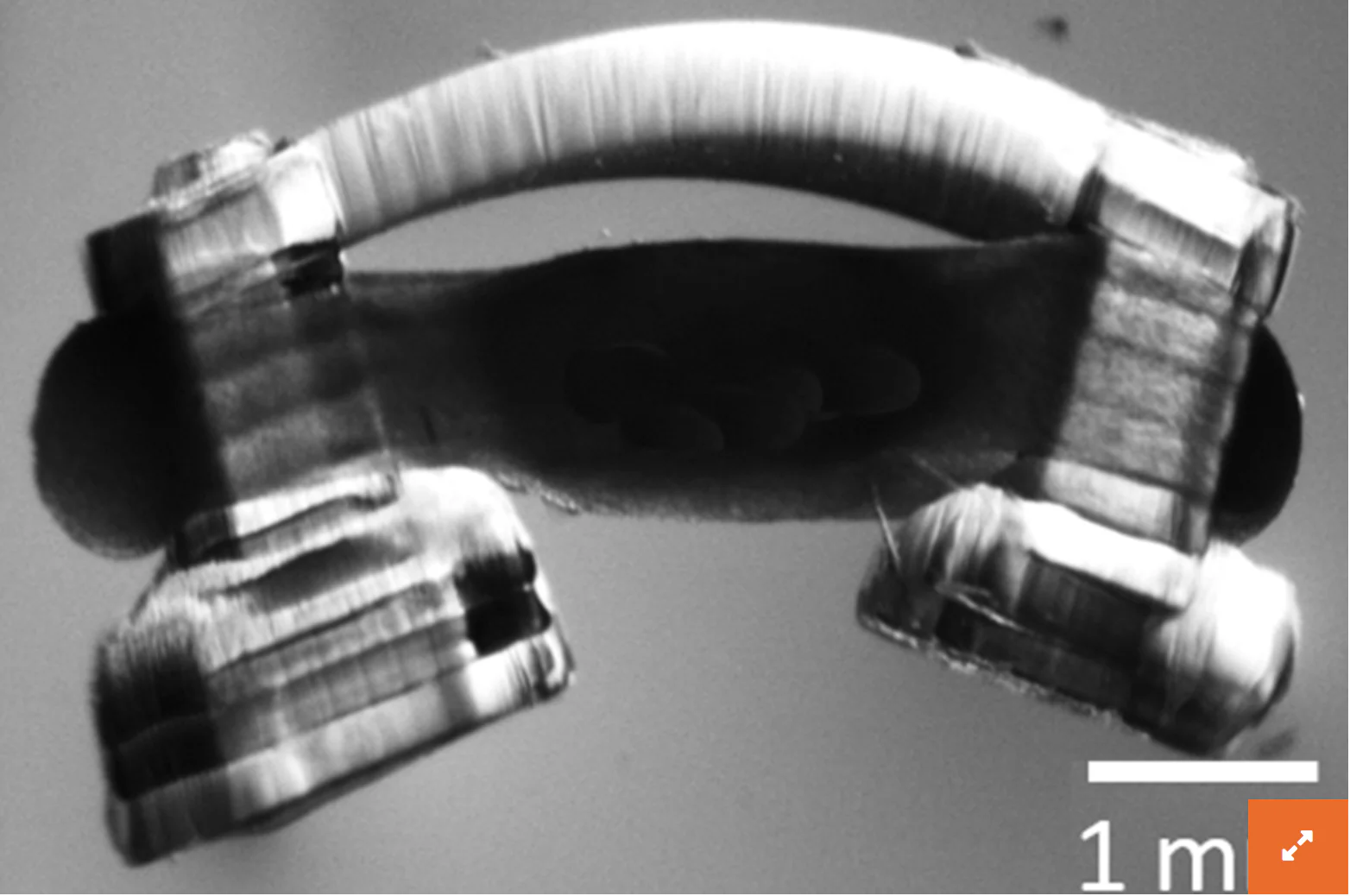
In a strange-sounding and important development in robotics, researchers at the University of Illinois at Urbana-Champaign have developed tiny “spinobots” capable of walking. They are powered by rat muscle and spinal cord tissue, which is present on the soft, 3D-printed hydrogel skeleton.
Prior to the new developments, biological robots relied on simple muscle contraction to move forward. With the use of the spinal cord in these new robots, they can walk with a more natural rhythm.
Martha Gillette is the study leader and professor of cell and developmental biology.
“These are the beginnings of a direction toward interactive biological devices that could have applications for neurocomputing and for restorative medicine,” Gillette said.
The findings were published in the journal APL Bioengineering.
Making the Spinobots
In order to build the spinobots, the researchers first printed the tiny skeleton. It had two posts that acted as legs, as well as a flexible “backbone.” The skeleton was then seeded with muscle cells that grew into muscle tissue, and a segment of lumbar spinal cord was taken from a rat and integrated into it.
Collin Kaufman is a graduate student and the first author of the paper.
“We specifically selected the lumbar spinal cord because previous work has demonstrated that it houses the circuits that control left-right alternation for lower limbs during walking,” said Kaufman. “From an engineering perspective, neurons are necessary to drive ever more complex, coordinated muscle movements. The most challenging obstacle for innervation was that nobody had ever cultured an intact rodent spinal cord before.”
Designing a Method to Integrate the Spinal Cord
The researchers developed a method in order to extract the intact spinal cord and culture it, as well as integrate it onto the robot while culturing the muscle and nerve tissues together. When doing this, they had to make sure the neurons formed junctions with the muscle.
After designing the new method, the researchers observed muscle contractions that took place in the spinobots. These meant that the neuro-muscular junctions did in fact form, and the two different types of cells were communicating. In order to make sure the spinal cord was functioning, which is needed for walking, the researchers used glutamate. Glutamate is a neurotransmitter that helps nerves to signal the muscle to contract.
The muscle contracted and the legs moved in a natural rhythm due to the glutamate, and once it was taken away, the spinobots did not walk anymore.
The next steps for the researchers include refining the movements of the spinobots, in a way so that they are even more natural. Their hope is that in vitro models of the peripheral nervous system can be created through the use of small-scale spinal cord integration.
“The development of an in vitro peripheral nervous system — spinal cord, outgrowths and innervated muscle — could allow researchers to study neurodegenerative diseases such as ALS in real time with greater ease of access to all the impacted components,” Kaufman said. “There are also a variety of ways that this technology could be used as a surgical training tool, from acting as a practice dummy made of real biological tissue to actually helping perform the surgery itself. These applications are, for now, in the fairly distant future, but the inclusion of an intact spinal cord circuit is an important step forward.”