Robotics
New System Improves Human-Robotic Interactions
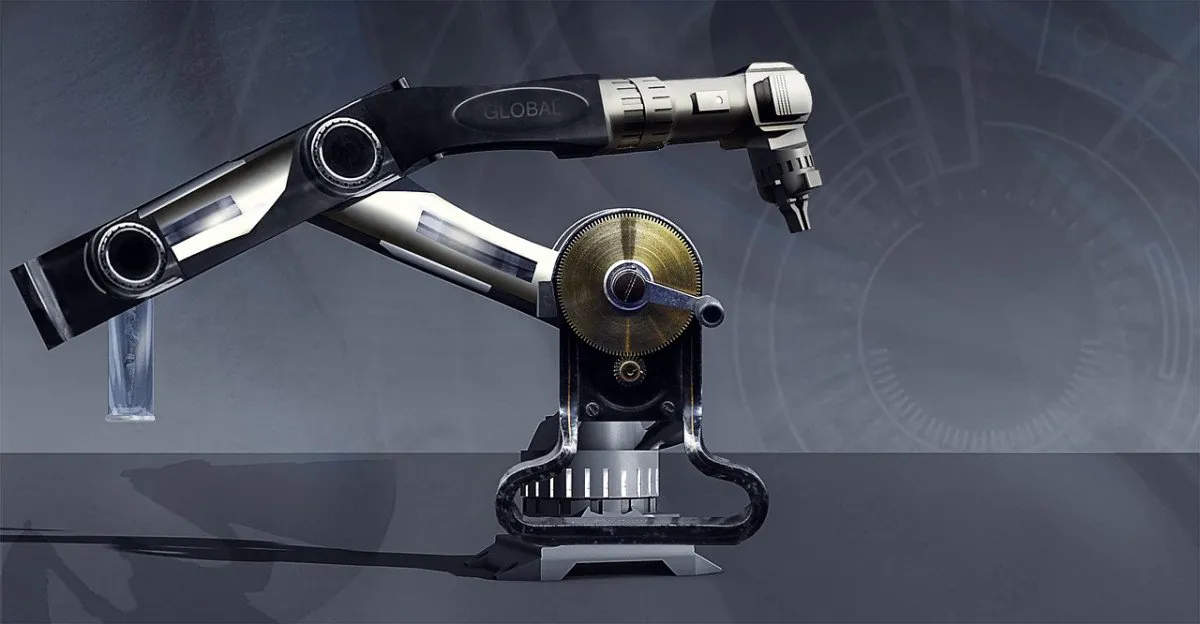
A team of researchers at the University of British Columbia Okanagan has used autonomous vehicle guidelines to develop a new system to improve human-robotic interactions.
Today’s research around automation and manufacturing is heavily focused on the way people interact safely with robots.
Robots in Manufacturing
Debasita Mukherjee is a doctoral student and lead author of the published study. She is one of the researchers at UBC’s Advanced Control and Intelligent Systems Laboratory who works to develop systems that enable safe human-robot interaction.
“It is incredibly important for robots in manufacturing to perform their tasks in the safest and most efficient method possible,” Mukherjee says. “In order to make these automated machines as smart as possible, we are developing systems that perceive their environments and carry out tasks in a similar manner as their human partners.”
Researchers use artificial intelligence and machine learning to guide the machines in order to develop systems like these, but the process can be complex.
Homayoun Najjaran is a mechanical engineering professor.
“Robots don't think or feel, so they need systems that capture and analyze their environment enabling them to respond,” says Dr. Najjaran. “Often those responses need to be in hundredths of a second to ensure the safety of humans in their vicinity.”
Industrial robots are usually programmed to operate at high speeds and perform specific tasks like welding and painting, but social robots are meant to assist individuals in service industries. The latter are more mobile, lightweight, and able to adapt to different environments.
Human-Robot Collaboration
The new field of research at UBCO’s School of Engineering is termed human-robot collaboration (HRC). It is making an impact on the manufacturing industry, especially since there is an increased interest in shared workspaces where robots and humans work side by side.
In an industrial setting, HRC can lead to intelligent, mobile robots that are aware of their surroundings and human partner. The team is working on getting these autonomous systems and machine learning technologies assimilated into HRC focused robotics, and they are doing so with the help of many organizations across the globe.
According to Mukherjee, the biggest challenge is adapting to uncertainty within the industrial setting. By using autonomous vehicle guidelines, there can be rules for functionality between humans and robots, as well as a way to test their effectiveness.
“Increasing automation levels is standardized and accepted by the automotive industry, but other industrial settings, while relatively static, don't have the same standards,” she says. “In the future, not only will industrial automated systems continue to use sensors to enable perception and communication similar to human capabilities, but they will also be adapting and communicating in real-time with their surroundings.”
All of this can enable robots to predict what humans and other robots will do, which helps them prepare the best response.
The team of researchers is now looking to develop systems that enable robots to function and respond outside of a prescribed environment.
“In an ‘open-world,' robots will need to deal with unexpected variables like people, structures, machines, and wildlife,” Mukherjee concludes. “We need to ensure they can do this correctly, efficiently and safely.”