Robotics
Flexible Robot âGrowsâ Like a Plant
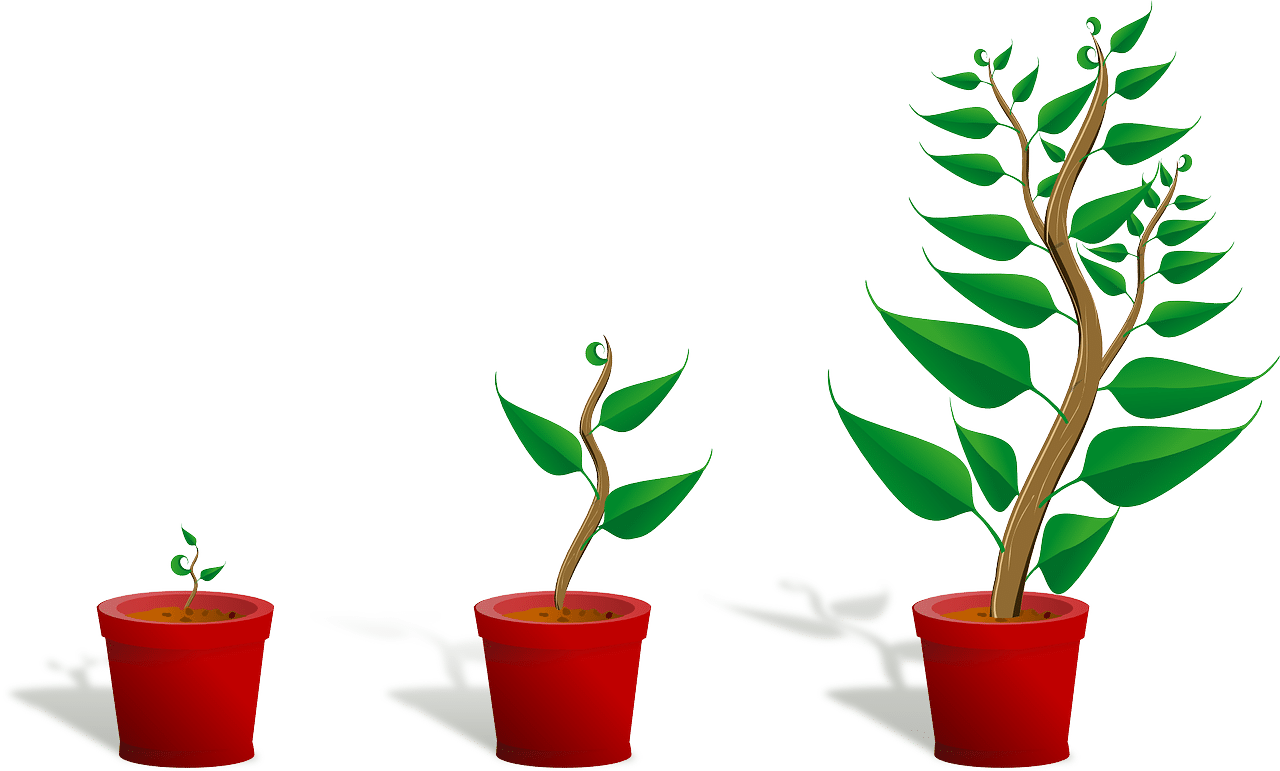
Engineers from MIT have designed a robot that can extend a chain-like appendage. This makes the robot extremely flexible, and it can configure itself in multiple different ways. At the same time, it is strong enough to support heavy weight or apply torque, making it capable of assembling parts in small spaces. After completing its tasks, the robot is able to retract the appendage, and it can extend it again with a different length and shape.Â
This newly developed robot can make a difference in areas like warehouses, where most of the robots are not able to put themselves in narrow spaces. The new plant-like robot can be used to grab products at the back of a shelf, and it can even move around a carâs engine parts to unscrew an oil cap.Â
The design was inspired by plants and the way they grow. In that process, nutrients are transported to the plantâs tip as a fluid. Once they reach the tip, they are converted into solid material that produces, a little at a time, a supportive stem.Â
The plant-like robot has a âgrowing pointâ or gearbox, which draws a loose chain of interlocking blocks into the box. Once there, gears lock the chain units together and release the chain, unit by unit, until it forms a rigid appendage.Â
Team of Engineers
The new robot was presented this week at the IEEE International Conference on Intelligent Robots and Systems (IROS) in Macau. In the future, the engineers would like to add on grippers, cameras, and sensors that could be mounted onto the gearbox. This would allow the robot to tighten a loose screw after making its way through an aircraftâs propulsion system. It could also retrieve a product without disturbing anything in the near surroundings.Â
Harry Asada is a professor of mechanical engineering at MIT.
“Think about changing the oil in your car,” Asada says. “After you open the engine roof, you have to be flexible enough to make sharp turns, left and right, to get to the oil filter, and then you have to be strong enough to twist the oil filter cap to remove it.”
Tongxi Yan is a former graduate student in Asadaâs lab, and he led the work.
“Now we have a robot that can potentially accomplish such tasks,” he says. “It can grow, retract, and grow again to a different shape, to adapt to its environment.”
The team of engineers also consisted of MIT graduate student Emily Kamienski and visiting scholar Seiichi Teshigawara.
Plant-Like Robot
After defining the different aspects of plant growth, the team looked to implement it into a robot.Â
“The realization of the robot is totally different from a real plant, but it exhibits the same kind of functionality, at a certain abstract level,” Asada says.
The gearbox was designed to represent the robotâs âgrowing tip,â which is the equivalent of a bud of a plant. That is where most nutrients flow up to the site, and the tip builds a rigid stem. The box consists of a system of gears and motors, and they pull up a fluidized material. For this robot, it is a sequence of 3-D printed plastic units that are connected with each other.Â
The robot is capable of being programmed to choose which units to lock together and which to leave unlocked. This allows it to form specific shapes and âgrowâ in specific directions.
“It can be locked in different places to be curved in different ways, and have a wide range of motions,” Yan says.
The chain is able to support a one-pound weight when locked and rigid. If a gripper were to be attached, the researchers believe it would be able to grow long enough to maneuver through a narrow space, and perform tasks such as unscrewing a cap.